Drilling crank for pilot bushing
#1
Drilling crank for pilot bushing
I want to convert my 65 442 auto. to stick shift. I would like to have the crank drilled for the pilot bushing. The motor doesn't need a rebuild. Can I remove the crank without pulling the heads? Motor is out of the car. Thank you.
#3
On my 455 conversion to a M21 4 speed I used a thinner pilot bearing for your application and did not have to take the motor apart. Making sure you have a little clearance between the input shaft and the back of the crank. This was done over 7 years ago and everything is still fine. The engine builders in this Club will chime in. I would wait to hear from them before taking the motor apart. I think I bought the bearing from Bill Travato.
#4
If it's out of the car you're already there. I mean yeah you can drop it out the bottom with the heads on but you'll still have to put the bottom end back together again and re-time it. Why go through all the trouble to drill a hole? Don't forget about hole for the Z-Bar also if not already there.
#6
On my 455 conversion to a M21 4 speed I used a thinner pilot bearing for your application and did not have to take the motor apart. Making sure you have a little clearance between the input shaft and the back of the crank. This was done over 7 years ago and everything is still fine. The engine builders in this Club will chime in. I would wait to hear from them before taking the motor apart. I think I bought the bearing from Bill Travato.
Do it right the first time.
#7
I believe it was Noah Melberg on FB he is Admin on 442, H/O page , looked like a big magnetic mounted commercial 1/2 drill , it wasnt a hand Craftsman 3/8" chuck ... he did it and drives it ask him.
#8
You can hack a rough hole for the clearance for a conversion bearing, but you will never be able to drill a pilot hole for the correct bearing correctly in the car.
Never.
I tried it, and the material in the crank is diamond hard.
Never.
I tried it, and the material in the crank is diamond hard.
#10
it can be done while the crank is in the motor,mag drill mounted on a stick flywheel.others will say no way but i've done it twice.drilled it for an early chevy v8 bushing and the bit cost me $80.00
#11
Now, to the OP's original question, yes you can pull the crank without disassembling the engine or removing the heads. The Chassis Service Manual even tells you how to do it.
#13
Sorry Joe, I don't buy the drilling the crank in the car.
Can you drill a hole in the crank in the car? = YES
Can you drill a hole in the crank to the tolerances required for the correct bearing? = NO
And, if the concentrically of the hole is off, the input shaft on the transmission will not release when the clutch pedal is pushed in, meaning that you won't be able to shift into reverse....and you have ruined your crank.
I encourage all the naysayers to give a try.....
Can you drill a hole in the crank in the car? = YES
Can you drill a hole in the crank to the tolerances required for the correct bearing? = NO
And, if the concentrically of the hole is off, the input shaft on the transmission will not release when the clutch pedal is pushed in, meaning that you won't be able to shift into reverse....and you have ruined your crank.
I encourage all the naysayers to give a try.....

#14
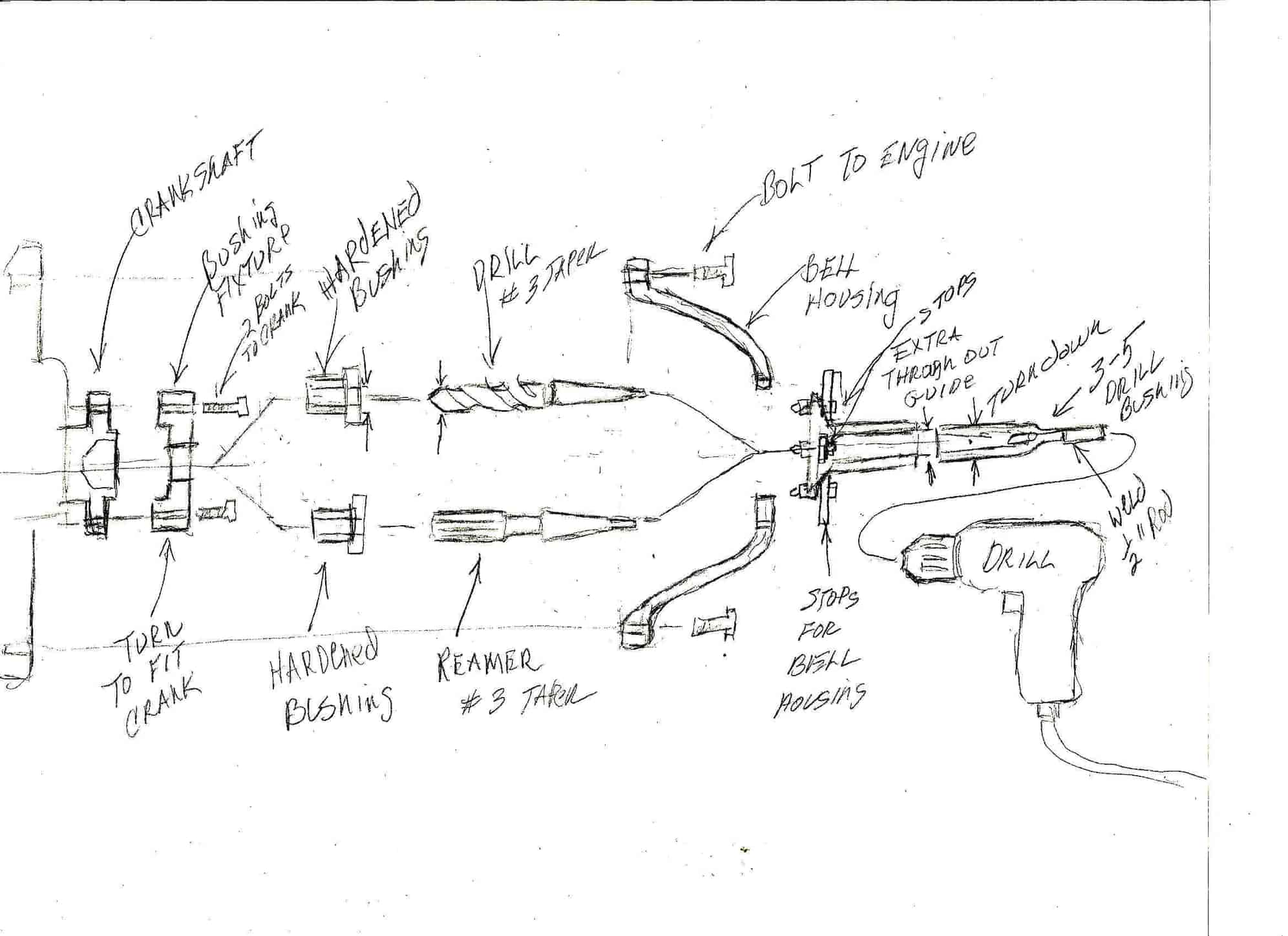
Sorry Joe, I don't buy the drilling the crank in the car.
Can you drill a hole in the crank in the car? = YES
Can you drill a hole in the crank to the tolerances required for the correct bearing? = NO
And, if the concentrically of the hole is off, the input shaft on the transmission will not release when the clutch pedal is pushed in, meaning that you won't be able to shift into reverse....and you have ruined your crank.
I encourage all the naysayers to give a try.....
Can you drill a hole in the crank in the car? = YES
Can you drill a hole in the crank to the tolerances required for the correct bearing? = NO
And, if the concentrically of the hole is off, the input shaft on the transmission will not release when the clutch pedal is pushed in, meaning that you won't be able to shift into reverse....and you have ruined your crank.
I encourage all the naysayers to give a try.....

Is it easier/cheaper to do it this way for a one-time use? Of course not. But if you plan to do more than one car, you will recoup the tooling investment.
#15
I did see the sketch, thanks.
However, You won't hold the tolerances required with that jig....but it will drill a hole.
The machine shop that drilled my crank did it with a precision end mill.
"I can drive nails in with a rock, but a nail gun works much better"
I would not attempt this with my car, buy your results may vary.
However, You won't hold the tolerances required with that jig....but it will drill a hole.
The machine shop that drilled my crank did it with a precision end mill.
"I can drive nails in with a rock, but a nail gun works much better"
I would not attempt this with my car, buy your results may vary.
#16
I've made LOTS of equally tight precision holes in aerospace structures and materials using a similar system and precision located drill bushings. It often isn't possible to drag a 12 ft diameter structure over to a milling machine.
#17
#18
I think I'm going to remove the crank and have it drilled by a machine shop. Joe I looked in the shop manual an saw how to remove the crank without removing the heads by just removing the rod bearing caps. Is there anything else I need to know before I dive into this project. Thank you!
#19
Since it has to come off, you MIGHTASWELL replace the oil pump.
Since the bearings come off, you MIGHTASWELL replace the rod bearings and main bearings.
With the crank out, you MIGHTASWELL put in a new neoprene rear main seal.
Since the timing chain needs to come off, you MIGHTASWELL replace the timing chain and gears and front seal.
Since the water pump needs to come off, you MIGHTASWELL replace the pump.
At that point, you're only 20 head bolts away from having the heads off for a valve job...
And at THAT point, you're only rings away from a total rebuild....
You begin to understand how a simple task turns into a body-off restoration.

#21
its soft as butter..(figure of speech)..i just did one myself..i thought the same thing..it wont work etc etc..i figured out a conversion bearing of my own after a day in a catalog..
i bought a huge 1/2 in bad *** drill etc..chucked a new but in and it cut like butter..the secret is low speed...i was amazed how easy too
i used an extended bearing..i didnt need accuracy, i needed clearance for the end of the input...i dont have pics but by the end of the week i will have them up with part numbers etc..i did it free handed..i used a depth micrometer to make sure i had what i needed...and i did it...again i didnt need accuracy..i needed depth clearance
im not saying what you are saying is wrong..im saying the crank is soft...and when you have more time than money..and people say it wont work..imma make it work
if i wouldnt have bought the drill and the bit..to make my 455 accept the bearing i chose...it would have cost me $5.85...and a few more for my machinist to adjust my bearing for me..which he wanted lunch not money
and i bought the drill because everyone said it was rock or diamond hard...it just isnt so
engine was out on the work bench..not in the car...and it was a complete running motor..and will be back in the car soon
i bought a huge 1/2 in bad *** drill etc..chucked a new but in and it cut like butter..the secret is low speed...i was amazed how easy too
i used an extended bearing..i didnt need accuracy, i needed clearance for the end of the input...i dont have pics but by the end of the week i will have them up with part numbers etc..i did it free handed..i used a depth micrometer to make sure i had what i needed...and i did it...again i didnt need accuracy..i needed depth clearance
im not saying what you are saying is wrong..im saying the crank is soft...and when you have more time than money..and people say it wont work..imma make it work
if i wouldnt have bought the drill and the bit..to make my 455 accept the bearing i chose...it would have cost me $5.85...and a few more for my machinist to adjust my bearing for me..which he wanted lunch not money
and i bought the drill because everyone said it was rock or diamond hard...it just isnt so
engine was out on the work bench..not in the car...and it was a complete running motor..and will be back in the car soon
Last edited by marxjunk; March 5th, 2016 at 05:27 PM.
#22
I have to disagree, I've used that conversion bearing 4 times since the early 2000s and never had a problem. All cars are still working fine. I think if they didn't work then you either didn't have clearance for the input shaft or it wasn't installed correctly. And also those cranks are not hard to drill, provided you don't skimp on a good drill bit and go slow.
#24
The recess on the AT crank is not deep enough to clear the input shaft tip. Your options are to either trim 1/2 - 3/4 inch from the input shaft or drill a clearance hole in the end of the crank. Since this hole is for clearance only, location and size are not important, so this can be done with the engine in the car with no issues.
#25
The recess on the AT crank is not deep enough to clear the input shaft tip. Your options are to either trim 1/2 - 3/4 inch from the input shaft or drill a clearance hole in the end of the crank. Since this hole is for clearance only, location and size are not important, so this can be done with the engine in the car with no issues.

#26
If I decide to drill for the conversion bearing and not shorten the shaft if for some reason the drilling doesn't go as planned can I risk damaging the crankshaft by damaging it where I have to sh**tcan the crank?
#28
i would never shorten the input..it kills the value of resale later..and admit it..you spend a chunk of change and then cut the input..that seems foolish...but..if you want to cut it..its case hardened..
put the trans in neutral shoot motor oil in the front bearing and use a fiber cut off wheel...and work the cutter around the tip...in other words dont just cut it off...if you oil the bearing friction will turn the input and it will cut it like its on a lathe...10 years ago i used a Hemi 4 speed in a chevy application..and there was no getting around cutting the input...looking back..pretty stupid cutting on a 2k trans to go racing...just sayin'
if i where going to do it in the car..id buy a good or rent a good angle drill..it would work and you can buy them with 1/2 in chuck when the chuck gets that big the speed goes down..or buy a foot pedal for an old singer sewing machine..you plug the pedal in the wall and the drill in it..i think its called a rheostat..it should be straight...and if you have good lighting..take your time..you can get it by eyeball..its for clearance the way i did it..not accuracy
new bit..slow speed the only way you could screw it up was to be drunk or fall asleep..it took me 10 minutes...
i figured out my depth by measuring a bell housing...then my trans from the housing to the tip added a 1/4 for growth...but a hillbilly could figure it out..install the bell..shove the trans on..use 2 long bolts for a guide and help support trans....when the trans bottoms on the bell..add 1/4
i checked it 3 times before i said good...shoved some thick red grease in there i put in the freezer..it was almost hard.. installed the bell and trans pulled it off and looked in the hole..VIOLA...easy..backwards as heck prob..but it worked...same as using clay for a valve to piston clearance...i just didnt have any clay
the crank is drilled at the factory for the converter clearance and mine, the center has a divot just like a drill bit went in there..so i felt i didnt need to figure out center..there it was...
i thought i needed to step the bits up..but when i shoved that first 1/4 in bit in there and the shavings poured out..i just stopped and used my final bit..no issues
put the trans in neutral shoot motor oil in the front bearing and use a fiber cut off wheel...and work the cutter around the tip...in other words dont just cut it off...if you oil the bearing friction will turn the input and it will cut it like its on a lathe...10 years ago i used a Hemi 4 speed in a chevy application..and there was no getting around cutting the input...looking back..pretty stupid cutting on a 2k trans to go racing...just sayin'
if i where going to do it in the car..id buy a good or rent a good angle drill..it would work and you can buy them with 1/2 in chuck when the chuck gets that big the speed goes down..or buy a foot pedal for an old singer sewing machine..you plug the pedal in the wall and the drill in it..i think its called a rheostat..it should be straight...and if you have good lighting..take your time..you can get it by eyeball..its for clearance the way i did it..not accuracy
new bit..slow speed the only way you could screw it up was to be drunk or fall asleep..it took me 10 minutes...
i figured out my depth by measuring a bell housing...then my trans from the housing to the tip added a 1/4 for growth...but a hillbilly could figure it out..install the bell..shove the trans on..use 2 long bolts for a guide and help support trans....when the trans bottoms on the bell..add 1/4
i checked it 3 times before i said good...shoved some thick red grease in there i put in the freezer..it was almost hard.. installed the bell and trans pulled it off and looked in the hole..VIOLA...easy..backwards as heck prob..but it worked...same as using clay for a valve to piston clearance...i just didnt have any clay
the crank is drilled at the factory for the converter clearance and mine, the center has a divot just like a drill bit went in there..so i felt i didnt need to figure out center..there it was...
i thought i needed to step the bits up..but when i shoved that first 1/4 in bit in there and the shavings poured out..i just stopped and used my final bit..no issues
Last edited by marxjunk; March 5th, 2016 at 05:29 PM.
#29
I cut the tip on one of them, can't remember why, but I guess I figured a new input shaft was only $50 or so. Used a dremel with a cutoff wheel then beveled the tip for easier installation of the tranny. For clearance I used a wad of clay, and just kept checking
#30
i remember the days of 50 dollar inputs..its way gone...i dont think its a bad thing to cut it..i just look forward...if you think the trans is living in there for ever then cut it..if you want to sell it later..can be detrimental...thats all i am saying..
looking back i would never cut one today..especially and 71 E-body coded hemi box..like i did...lol...it meant nothing to me but they are freakin' strong and i wanted to race a 4 speed....and i did...and i blowd it up too...sweet to see parts all over the ground at the starting line...i went to a toplader out of a 428 super cobrajet torino and never broke it.....they are the stongest i think on the planet...
this was way back...there where no aftermarket 4 speeds...maybe the doug nash but sooo expensive..blew up 2 liberty geared t-10s...lots of fun..i'll tell ya that,,but that top loader....was an anvil..beat on it..torture it..beat on it some more...never flinched...
oh crap..i'm rambling on again...
looking back i would never cut one today..especially and 71 E-body coded hemi box..like i did...lol...it meant nothing to me but they are freakin' strong and i wanted to race a 4 speed....and i did...and i blowd it up too...sweet to see parts all over the ground at the starting line...i went to a toplader out of a 428 super cobrajet torino and never broke it.....they are the stongest i think on the planet...
this was way back...there where no aftermarket 4 speeds...maybe the doug nash but sooo expensive..blew up 2 liberty geared t-10s...lots of fun..i'll tell ya that,,but that top loader....was an anvil..beat on it..torture it..beat on it some more...never flinched...
oh crap..i'm rambling on again...
#31
I guess I got lucky? As mentioned I bought the thinner pilot bearing, used a little clay to make sure I had a air gap between the input shaft and the back of the crank. Dry fit everything several times and has been fine for years. I totally understand that if I did not have the "air gap" I would have pulled the crank.
Thread
Thread Starter
Forum
Replies
Last Post
dads72
Small Blocks
7
March 25th, 2015 03:12 AM
young olds
Transmission
4
August 23rd, 2013 05:26 PM