VIN rivets
#2
#4
Back in the 80's I worked at Texas Instruments. The North building had all of the hardware in what was called the pipe frame floor. There was a bin, open to anyone, that had the exact rivets used to attach the vin tags. Should have grabbed me a whole handful.
#5
I would love to see some video of cars being built.
I would have assumed that all A body cars would have basically the same assembly process. Obviously since parts are assembled differently deterrent different model/makes the actual PROCESS would be different, but I assumed the order would be similar.
The point to my thoughts, every car has the VIN tag in the same location. Why would the rivets be installed differently? I would think if the rivets go in from the top, they would be installed before the glass. If the go in from the bottom, I’d assume the were installed before the dash.
I guess since I work in a factory I’m a little more tuned and inquisitive to the thought process of mass production.
#6
I don’t know why but the windshields in the Lansing cars were pre-installed before the rest of the car was assembled but in BOP plants the windshields were installed after the VIN was installed. This info came from Dave H about 20 years ago.
#7
I would love to see some video of cars being built.
I would have assumed that all A body cars would have basically the same assembly process. Obviously since parts are assembled differently deterrent different model/makes the actual PROCESS would be different, but I assumed the order would be similar.
The point to my thoughts, every car has the VIN tag in the same location. Why would the rivets be installed differently? I would think if the rivets go in from the top, they would be installed before the glass. If the go in from the bottom, I’d assume the were installed before the dash.
I guess since I work in a factory I’m a little more tuned and inquisitive to the thought process of mass production.
I would have assumed that all A body cars would have basically the same assembly process. Obviously since parts are assembled differently deterrent different model/makes the actual PROCESS would be different, but I assumed the order would be similar.
The point to my thoughts, every car has the VIN tag in the same location. Why would the rivets be installed differently? I would think if the rivets go in from the top, they would be installed before the glass. If the go in from the bottom, I’d assume the were installed before the dash.
I guess since I work in a factory I’m a little more tuned and inquisitive to the thought process of mass production.

#8
As a apprentice toolmaker early 1980 we went to Fisher auto body for a tour.
Nothing was running in the plant, everyone was in cafeteria as they made quota for the day and did not need to work any longer.
Thats the Union for ya.
And we wonder why they shut down.
Nothing was running in the plant, everyone was in cafeteria as they made quota for the day and did not need to work any longer.
Thats the Union for ya.
And we wonder why they shut down.
#10
Excellent ! 23,000,000 gallons of paint in a single year !
#11
I work for Ford & our vin tags are installed before the windshields are decked. Back in the 90s when we were building minivans I worked near the station where they attached the vin tags. There was a large box full of thousands of the special rosette rivets, They weren't secured in anyway, anyone could walk by & grab a handful if they wanted! They were left out even when the shifts were over.
#12
#13
i was thinking the same thing, but didn’t want to open a can of worms with the “union workers are lazy” chest thumping crowd.
While I don’t work in a vehicle assembly plant, I know enough people that have or currently do. If those assembly lines are stopped, it’s for a good reason!! They don’t stop assembly lines once they get a certain number!
I have worked for 23 years in the transmission plant for Chrysler. They don’t voluntarily shut off the line for transmission assembly, ever! If it’s off during regular production, it’s due to a mechanical breakdown or production problem.
Having said that, there is a target production rate. That’s the number of units that can be built in a 8 hour shift is everything goes perfect, zero stoppage, every operation goes exactly right, no machine breakdown, etc. I’m sure you can imagine how often that actually happens.
In my 23 years at that factory, I have spent the majority in sub-assembly. Things like valve body assembly, pump assembly, clutch and planetary assembly. Those lines do usually have a production rate. I liked to do the physically challenging work that nobody else wanted, and liked to get good at it, just to hit that number and relax the rest of the shift. If I can do the job in 6.5 hours that takes someone else the entire shift to do, and do it correctly and accurately, sign me up!!
And before anyone starts in with “getting paid to do nothing” to me it’s no different that turning wrenches and beating flat-rate, or piece-rate pay scale, or any other production based pay. It takes lots of time and effort to get good at certain jobs.
I take pride in what I do. I REFUSE to keep quiet when machines or parts are junk. There are a lot of things that go on in a big factory that just make m blood boil, too many corporate decisions made to look good on a spreadsheet. Decisions that hourly guys like me have zero control over. Things that make people outside of the factory shake their heads in absolute disbelief.
if anyone really is interested in hearing some of the bullshit stories I’ll be more than happy to share. I’m sure everyone has seen stupid things in their work also. Maybe an idea for a new thread?
#14
My friend assembles jet engines his whole life (union).
He has a CRT that guides EVERY part by serial number, install, recheck, document.
THEN Wait for the CRT to advance him to the next same new part install.
> no room for mistakes
8 hours every 8 hour day
he says he could do his 8 hour shift in much less time but - you know - you can't just pull over if your jet engine breaks
He has a CRT that guides EVERY part by serial number, install, recheck, document.
THEN Wait for the CRT to advance him to the next same new part install.
> no room for mistakes
8 hours every 8 hour day
he says he could do his 8 hour shift in much less time but - you know - you can't just pull over if your jet engine breaks
#15
My friend assembles jet engines his whole life (union).
He has a CRT that guides EVERY part by serial number, install, recheck, document.
THEN Wait for the CRT to advance him to the next same new part install.
> no room for mistakes
8 hours every 8 hour day
he says he could do his 8 hour shift in much less time but - you know - you can't just pull over if your jet engine breaks
He has a CRT that guides EVERY part by serial number, install, recheck, document.
THEN Wait for the CRT to advance him to the next same new part install.
> no room for mistakes
8 hours every 8 hour day
he says he could do his 8 hour shift in much less time but - you know - you can't just pull over if your jet engine breaks
We make A lot of aircraft bearings. Your friend probably has used parts I've made. Some parts we just run them but a few if the highly sensitive bearings ever piece has a serial number or code that can be traced to when where who touched what and when.
#16
My friend assembles jet engines his whole life (union).
He has a CRT that guides EVERY part by serial number, install, recheck, document.
THEN Wait for the CRT to advance him to the next same new part install.
> no room for mistakes
8 hours every 8 hour day
he says he could do his 8 hour shift in much less time but - you know - you can't just pull over if your jet engine breaks
He has a CRT that guides EVERY part by serial number, install, recheck, document.
THEN Wait for the CRT to advance him to the next same new part install.
> no room for mistakes
8 hours every 8 hour day
he says he could do his 8 hour shift in much less time but - you know - you can't just pull over if your jet engine breaks
I spent several years working on the clutch line that made the clutch assembly for the TES 4 speed transmission (the Chrysler minivan, Neon, other 4speed fwd transmissions). When the 42RLE (Jeep wrangler) and the 42LE transmissions (the Dodge Intrepid and other LH cars) came out each used a version of the clutch my line made. While they were similar clutch packs, they each used different pistons and friction stack up. To eliminate putting the wrong parts in the different model they installed a tv camera that looked for a specific side profile view of the parts. At the time I’m sure it was a big deal, now they use that stuff everywhere.
They also added a bar code to each finished clutch assembly, along with sensors on the assembly line to identify the beginning and end of each model change. They had sensors on the actual transmission assembly line that scanned each bar code to ensure the proper assembly went into each trans. That stuff is common now, at the time we thought that was pretty slick!
Quality engineering took the quality standards pretty seriously. But your absolutely correct, planes can’t pull over to a cloud if there is problems!!!
The Dept that made that transmission ceased production last month.
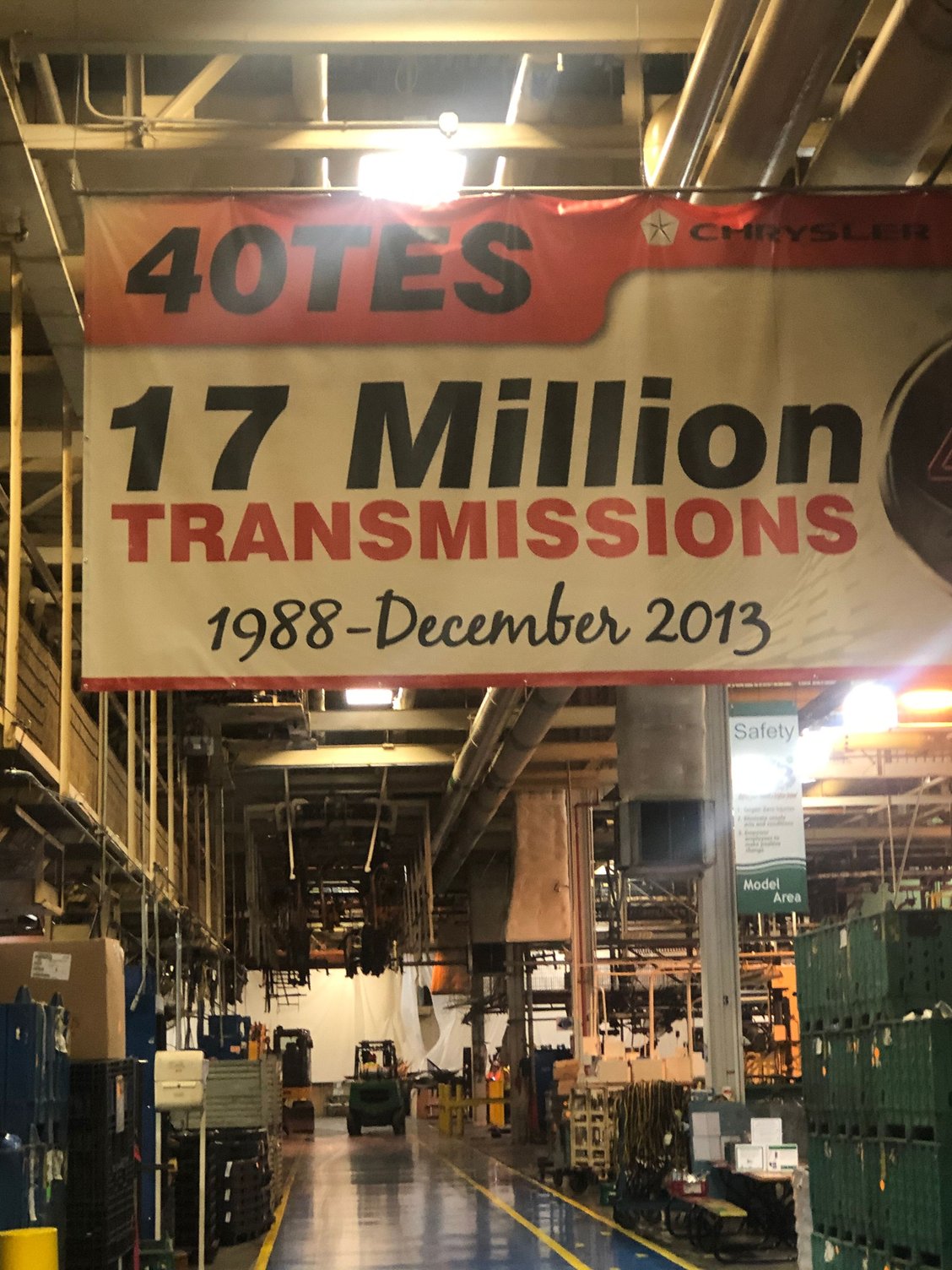
I’d be interested in knowing what the total production was from that line. I’d REALLY like to know how many clutch assemblies the clutch line built. Like I said, the clutch line made clutches for the 404,604 (which is still currently in production), 42LE, and 42RLE trans.
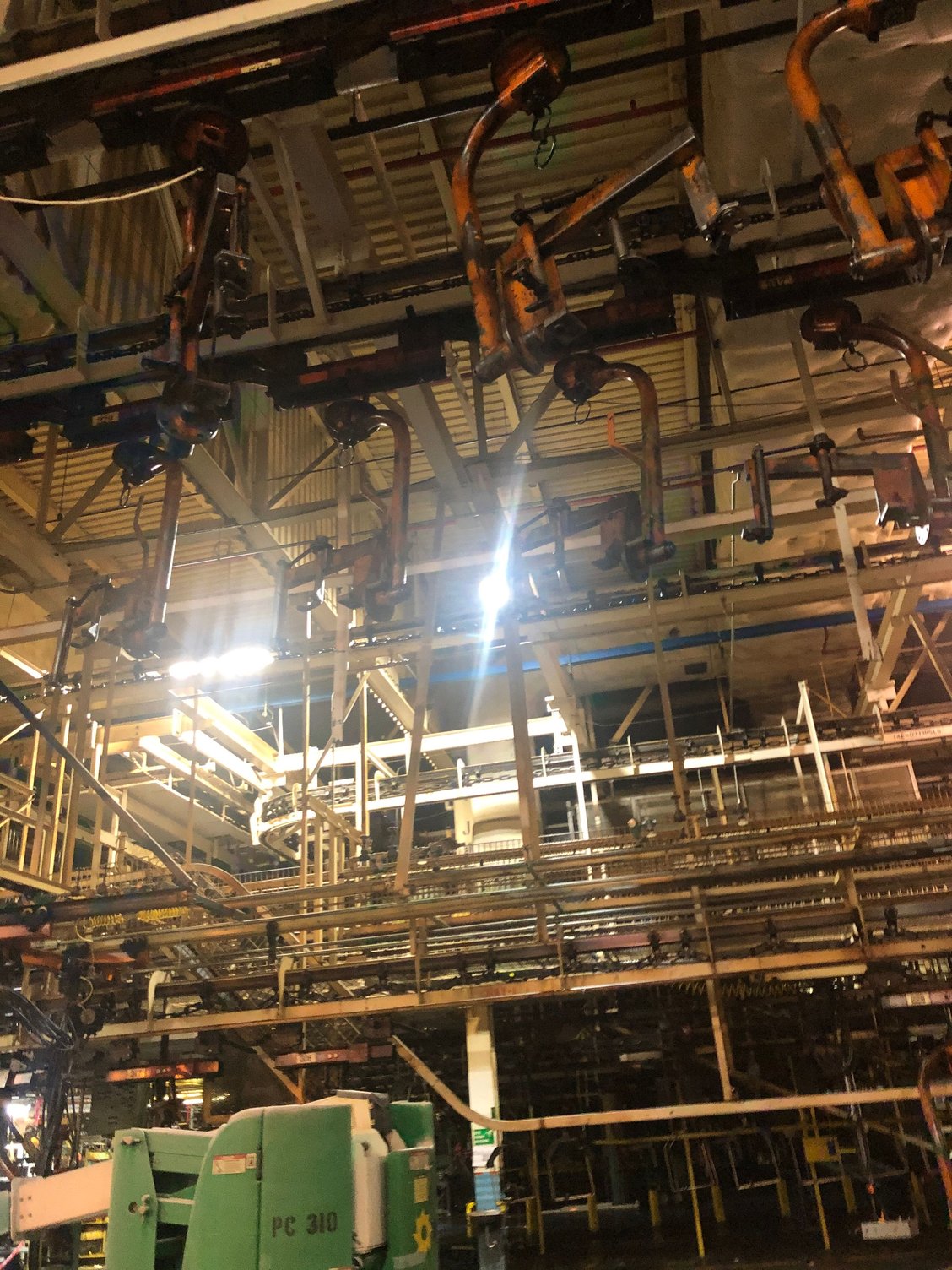
Some of the overhead conveyers that the transmissions ran on.
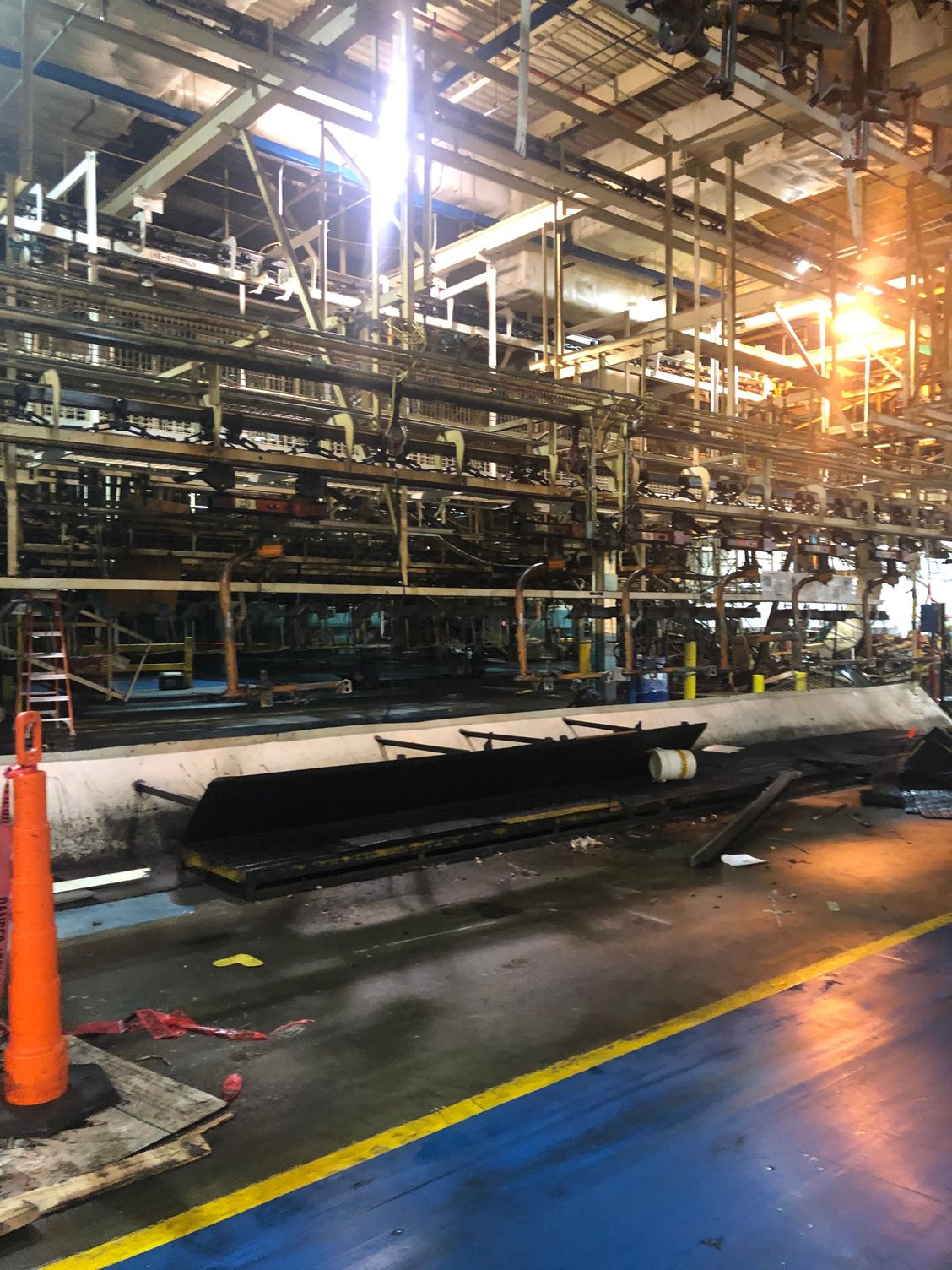
All this equipment being scrapped to make room for a engine block machining line.
#18
Kokomo is a happening place. This was the home of Delco electronics headquarters. Every radio, voltage regulator, pcm, and countless other electronic components in every GM car up until the early 2000s was made here. At its highest employment, 17000 people worked in one of the 5 Delco plants here. Unfortunately, all that’s left now is one main building and the engineering buildings. About 300 people work there now. My dad worked at Delco for 38 years until the last big downsize forced him out. He says he avoids driving past the building, he’s pretty bitter about the the way things went the last few years he worked there.
https://en.wikipedia.org/wiki/Kokomo,_Indiana
Thread
Thread Starter
Forum
Replies
Last Post